Check out this easy to understand video on endmill basics. To purchase endmills from Western Tool Company, Click here (westerntoolco.com).
Western Tool Company is located in Arvada Colorado and specializes in Maintenance, Repair and Operations Products. We ship all over the United States.
Wednesday, May 30, 2018
Tuesday, May 29, 2018
WHAT ARE CARBIDE CUTTING TOOLS?
Carbide Cutting Tools
Guest Post By Bo BoshenoveCarbide cutting tools are tools that have the end of the tool, or the tip, coated with carbide, and is used to make cuts through some of the toughest materials known. So, how did we arrive at the place where carbide was invented and the use became so widespread? Well, carbide was a derivative of hard metal.
![]() |
Westerntoolco.com 303-422-3413 |
Until the turn of the century, and the onset of the industrial revolution, hard metal was the best the industry had to offer.
Unfortunately, the best the industry had to offer wasn't all that good. Scientists and metal workers had already devoted a great deal of time to the creation of a harder substance, when, along came carbide. What scientists and metal workers discovered, was that if you decrease the iron (Fe) with harder carbide substances, you got a harder cutting tool.
A metal known as tungsten carbide was introduced into the market during the 1920s and you have the invention of carbide cutting tools. The industrial world was rapidly changed, and as you can see, today we have benefited greatly from this discovery.
For a complete listing of our cutting tools, visit our catalog at Westerntoolco.com
Along with the introduction of carbide cutting tools, came the industrial revolution and although there was some modification of machinery, the industry was welcoming this new tool with open arms. The hotter the cutting process, the harder the cutting tool needed to be, and with the progress of machinery, tools, and man's hunger for automation, the carbide tool filled a much needed space.
The hard carbide particles most often used in carbide cutting tools are those of tungsten carbide, titanium carbide and tantalum carbide grains. The carbide cutting tools are made by using a metallurgical powder, pressing it into a die, and then heating it in a furnace to a temperature of at least 1400 degrees Celsius. That's extremely hot, but carbide is extremely tough!
_____________________________
Learn more about cutting tool options at Bo's cutting tool directory Carbide Cutting Tools [http://www.Cuttingtools-co.info].
Article Source: http://EzineArticles.com/expert/Bo_Boshenove/32618
http://EzineArticles.com/?Carbide-Cutting-Tools&id=181199
Monday, May 28, 2018
HERMES ABRASIVES: Cylindrical Grinding - Western Tool Company
Western Tool Company is an authorized dealer of Hermes Abrasives. Check out this video on cylindrical grinding.
To purchase Hermes Abrasives, click here:
Westerntoolco.com (Hermes Abrasives)
To purchase Hermes Abrasives, click here:
Westerntoolco.com (Hermes Abrasives)
Sunday, May 27, 2018
GEMINI INDUSTRIAL COATINGS, LACQUERS AND STAINS from Western Tool Company
Western Tool Company is Colorado's exclusive distributor of Gemini industrial coatings, lacquers and stains. Here is a video about Gemini Industries. If you're in Colorado, give us a call at 303-422-3413 or visit our website at westerntoolco.com for more information about our product lines.
Friday, May 25, 2018
AIR SANDERS, WHAT YOU NEED TO KNOW from Western Tool Company
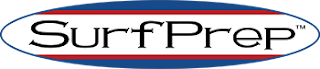
After operating an Air Tool Repair Service Center for 10 years, repairing and rebuilding thousands of sanders of various brands, I put this simple question/answer sheet together to address often asked questions to ensure many years of long life for your investment.
Think of the investment made when purchasing air sanders and the daily use and operation you plan on putting them through. As you do, now think of the vehicle you depend on and drive for daily transportation. Vehicles, like air tools, have wearable parts that require regular maintenance. Tires… purchasing new tires I’m sure is not something you look forward to. If you choose not to rotate your tires or not keep them properly inflated, plan on buying new tires on a more frequent basis. Some drivers, depending on the quality of tires, will get 65k miles of wear with simple maintenance where
another driver will be lucky to get 35k miles of life. Attention to the care and maintenance of your SurfPrep Air Sanders investment will yield twice the life on your purchase, just like that of your tires. The same can be said of oil changes and the quality of oil chosen for your vehicle.
SurfPrep Air Tools have been designed and built with the highest quality materials in order to yield minimal operational costs at fractions of pennies for daily use. Wearable parts have been engineered with the tightest tolerances meaning smooth operation, long life and minimal operator fatigue.
Click here for our Surfprep inventory and to buy Surfprep Products (westerntoolco.com)
OEM requirements:
- All SurfPrep Sanders (12,000 RPM/3.4 CFM & 10,000 RPM/3.1 CFM) require 90 PSI.
- Why, after a period of time, does my sander slow down and lose its rate of cut even though the exhaust parts are in place, I have clean air, 90 PSI and 3.4 CFM feeding the sander?
- When am I supposed to oil my sander and where do I put the oil?
- When I activate or depress the throttle lever to run my sander, why does air just blow through and out the exhaust and my tool does not run?
(2) The incorrect oil has been used causing the vanes to “stick” in place in the rotor and not float out to catch the airflow driving the counter balance.
(3) Contaminated Air causes the Vanes to “stick” in place in the rotor.
(4) Missing exhaust parts allows sanded substrate to re-enter back through the exhaust port mixing w/ oil causing a sludge to form.
- What happens if I do not lubricate/oil my sander?
- What happens if my black muffler cap/external dust filter breaks off, or I decide to remove it?
- What if I operate my SurfPrep 3” x 4” with pressures over 90 PSI?
- Why is there a mist of water spraying out of my exhaust cap?
- Why is oil dripping from my exhaust cap?
- When should I replace the White (12,000RPM) or Black Foam (10,000RPM) external dust filter on my sander?
- When I depress or activate the throttle lever to sand, while my sander is sitting on the substrate I’m sanding, why does the motor run but the backup pad does not spin?
- What happens if I run (6) sanders in a drop station off an airline, providing enough PSI to operate all (6) sanders simultaneously at 90 PSI and then I only run (2) of the (6) sanders off the same airline with the PSI still set for (6) sanders?
- How can I improve the ergonomics and handling of my sander?
- I have a sander that when the throttle lever has been released, the backup pad still rotates, continuing to run until I grab it to stop the rotation, why?
- Can I use oil, other than what is recommended, in my sander?
- What is the warranty for SurfPrep Air Sanders?
- Can I operate (1) sander off my 80 gallon, (2) stage, 5HP Compressor?
- The moment I connect my air supply line to my sander it immediately begins running and I haven’t even depressed or activated the throttle lever, why?
Remember:
- SurfPrep Random Orbital Sanders, “Round” (3”/5”/6”) with a 3/16” orbit are 12,000 RPM & aggressive, meaning a leveling tool. A 3/32” orbit is slightly less aggressive simply due to the tighter orbit pattern.
- SurfPrep Orbital Sanders, “Rectangular” 3” x 4” with a 3mm orbit 10,000 RPM can be set up to act Semi Aggressive w/ a “pad saver” and SurfPrep FILM, but because of design are less aggressive than either the Round 3/16” or 3/32” sanders. This sander is more of a Finishing Sander.
- All Air tools require regular lubrication
- Install air flow regulators with water separation filters in all sanding areas to regulate air flow and remove any compressed air condensation.
- Air pressure above 90 PSI running through the 3” x 4” sander will result in erratic behavior that can cause a rattling noise while sanding.
- When laying out your shop or production facility, make certain to “loop” your air supply line as opposed to “dead-heading” individual lines to different stations. Then run legs off your “loop”. A side benefit to this layout is the loop acts as an additional “storage tank”.
- All O.E.M. parts are available from your distributor.
Thursday, May 24, 2018
CHEMETALL MACHINE COOLANTS from Western Tool Company
Chemetall is one of our trusted product lines of machine coolants. Check out their video on their 6 point total values system. To buy Chemetall products, click here.
Wednesday, May 23, 2018
PROLONGING THE LIFE OF TOOLS from Western Tool Company
Prolonging the Life of Tools When Machining Titanium
By E Ethier
Machining titanium can be very hard on the tools that you use. Often, the machines run down and break quite easily, but there are measures you can take to prolong the life of your tools when you are machining the titanium to make products.
Below is a few tips on things you can do to prevent machine malfunction. These range from coolant to new tools and if you follow them, you will no further problems when you are machining titanium.
Use a Coolant
You must use a coolant when you are machining titanium. If you don't the tool is likely to chip and the sheet might become over heated. Using a coolant helps keep the sheet cool and it acts a lubricant for the tool.
When using a coolant, make sure that you look out for chips that are machined away from the sheet
you are cutting. Sometimes with the coolant, it does not cool or flush the chips away properly so they can become jammed in the tool, or result in re-chipping. This is why you have to make sure that the chips are properly evacuated from the tooling area.
If you are using a proper coolant, you might think that it will be enough lubrication so that you will not have any further issues, but, you have to make sure that there is enough pressure in the implementation of the coolant, so it results in the required amount of lubricant. If there isn't enough pressure, this could lead to the tool failing and the titanium will wear down during the machining process.
When titanium is being machined, the tip of the tool can get very hot and this can lead to problems with how the coolant is applied during the process. If the tool is very hot, the coolant with evaporate before it even makes contact with the sheet. This will also lead to tool failure and a loss of accuracy when it comes to the item you are making. To overcome this, think about purchasing a new tool that has localised pressure.
Quality of Machine Tool
For some companies, they try and do their machining at the lowest possible costs. They have to cut costs somewhere and they often do this by buying machines that cost less. What do you think happens when you are using a machine often and you have sacrificed on the quality of the machine? Yes, it will break often and you will have to buy new machines more often.
When machining titanium, the tool will get hot and it is even more likely to break. So, the only option you have is to spend more money on a better machine. Make sure the tool has a rigid work holder that remains stiff. In titanium machining, the sheet that you use is going to vibrate, there is no getting around that, so make sure that the tool you buy has been designed well, with stability in mind.
Which Machine?
If you are new to machining titanium, the task of buying the right tool can be daunting. You will probably have no idea what to buy. So, go on websites and look for machines that were made specifically for cutting hard materials.
Once you have found one, read the reviews on the machine. If you still aren't sure if the machine is suitable, then do a Google search on the machine and look of forums that technicians frequent. They will have a better idea if the machine is suitable for machining titanium or not and their opinion will be more reliable than product reviews.
Supra Alloys was founded in 1965 by George Esseff Sr. The company is one of the leading distributors of titanium in the United States of America. They supply titanium to the medical, aerospace and chemical industries, among others. The company was bought by Lawrence Holdings in February 2015 and have been going strong since then. They have a policy by where they are committed to service, reliability and quality, with a customer service team who are trained with the knowledge to help their customers with any titanium related queries, they can even help with technical issues. You can visit their website at http://www.supraalloys.com
Article Source: http://EzineArticles.com/expert/E_Ethier/1680400
http://EzineArticles.com/?Prolonging-the-Life-of-Tools-When-Machining-Titanium&id=8144189
By E Ethier
Machining titanium can be very hard on the tools that you use. Often, the machines run down and break quite easily, but there are measures you can take to prolong the life of your tools when you are machining the titanium to make products.
Below is a few tips on things you can do to prevent machine malfunction. These range from coolant to new tools and if you follow them, you will no further problems when you are machining titanium.
Use a Coolant
You must use a coolant when you are machining titanium. If you don't the tool is likely to chip and the sheet might become over heated. Using a coolant helps keep the sheet cool and it acts a lubricant for the tool.
When using a coolant, make sure that you look out for chips that are machined away from the sheet
For Chemetall Coolant, click here (westerntoolco.com)
you are cutting. Sometimes with the coolant, it does not cool or flush the chips away properly so they can become jammed in the tool, or result in re-chipping. This is why you have to make sure that the chips are properly evacuated from the tooling area.
If you are using a proper coolant, you might think that it will be enough lubrication so that you will not have any further issues, but, you have to make sure that there is enough pressure in the implementation of the coolant, so it results in the required amount of lubricant. If there isn't enough pressure, this could lead to the tool failing and the titanium will wear down during the machining process.
When titanium is being machined, the tip of the tool can get very hot and this can lead to problems with how the coolant is applied during the process. If the tool is very hot, the coolant with evaporate before it even makes contact with the sheet. This will also lead to tool failure and a loss of accuracy when it comes to the item you are making. To overcome this, think about purchasing a new tool that has localised pressure.
Quality of Machine Tool
For some companies, they try and do their machining at the lowest possible costs. They have to cut costs somewhere and they often do this by buying machines that cost less. What do you think happens when you are using a machine often and you have sacrificed on the quality of the machine? Yes, it will break often and you will have to buy new machines more often.
When machining titanium, the tool will get hot and it is even more likely to break. So, the only option you have is to spend more money on a better machine. Make sure the tool has a rigid work holder that remains stiff. In titanium machining, the sheet that you use is going to vibrate, there is no getting around that, so make sure that the tool you buy has been designed well, with stability in mind.
Which Machine?
If you are new to machining titanium, the task of buying the right tool can be daunting. You will probably have no idea what to buy. So, go on websites and look for machines that were made specifically for cutting hard materials.
Once you have found one, read the reviews on the machine. If you still aren't sure if the machine is suitable, then do a Google search on the machine and look of forums that technicians frequent. They will have a better idea if the machine is suitable for machining titanium or not and their opinion will be more reliable than product reviews.
Supra Alloys was founded in 1965 by George Esseff Sr. The company is one of the leading distributors of titanium in the United States of America. They supply titanium to the medical, aerospace and chemical industries, among others. The company was bought by Lawrence Holdings in February 2015 and have been going strong since then. They have a policy by where they are committed to service, reliability and quality, with a customer service team who are trained with the knowledge to help their customers with any titanium related queries, they can even help with technical issues. You can visit their website at http://www.supraalloys.com
Article Source: http://EzineArticles.com/expert/E_Ethier/1680400
http://EzineArticles.com/?Prolonging-the-Life-of-Tools-When-Machining-Titanium&id=8144189
Tuesday, May 22, 2018
CARBIDE INSERTS: HOW THEY ARE MADE from Western Tool Company
How Carbide Inserts Are Made
Guest Post By Marjorie Steele
Manufacturing and machining shops that rely on carbide inserts for high speed tooling typically go through thousands of inserts each year. Machine operators work with many inserts each day, relying on their complex combination of chemistry and geometry to provide the cutting edges needed for precision, high speed production. Understanding how carbide tools are made and how the insert manufacturing processes influences their capabilities can help machine operators and manufacturers better understand their tools and overall processes.
What Carbide Inserts Are Made From
Most carbide inserts consist of cemented carbide, which is made from a combination of cobalt and tungsten carbide. Tungsten carbide's hard particles within the insert provide the insert with its qualities of hardness, and cobalt acts as the binding agent, holding the materials solidly together. The size of the tungsten grains being used affects the insert's hardness; larger grains (3-5 microns) result in softer, more quickly worn insert materials, while small grains (less than 1 micron) result in extremely hard, wear resistant inserts. The harder the tool, the more brittle it will be. When machining metals of exceptional hardness, harder inserts with smaller grains are typically used, while softer inserts are used most often in machining processes with interrupted cuts, which call for less brittle, tougher materials. The ratio of cobalt to tungsten carbide also influences carbide inserts' hardness levels; cobalt is softer, so the more cobalt an insert contains, the softer it will be.
The Insert Manufacturing Process
After the engineer has determined what level of hardness needs to be achieved, the manufacturing process starts with powdered raw materials. Powdered tungsten, cobalt and carbon are milled and blended together with alcohol and water, creating a thick slurry. This substance is put into a dryer, which evaporates the liquids, leaving a thoroughly mixed powder. Carbide inserts then undergo a sintering process in which they are mixed with a polymer to form a paste, pressed into insert-shaped dies and placed in a high-heat furnace to be sintered. The polymer is melted out of the inserts during this step, and the inserts shrink.
Coating Carbide Inserts
For most machining applications, coated carbide inserts are used. Coatings provide added levels of hardness and wear resistance which become necessary, especially during high-speed machining or machining of extremely hard metals. Most carbide tools are coated using chemical vapor deposition, in which a metal is ionized with electrical currents and applied to the inserts in the form of vaporized condensation. Another common process is physical vapor deposition, which creates thinner coating layers resulting in sharper cutting edges ideal for machining hardened steel and titanium.
Christopher Kyle is president of Knight Carbide, a Michigan-based manufacturer of tungsten carbide inserts. Knight Carbide specializes in custom insert engineering and manufacturing. To learn more about carbide insert technology, visit http://www.knightcarbide.com.
Article Source: http://EzineArticles.com/expert/Marjorie_Steele/724749
http://EzineArticles.com/?How-Carbide-Inserts-Are-Made&id=6212832
Guest Post By Marjorie Steele
Manufacturing and machining shops that rely on carbide inserts for high speed tooling typically go through thousands of inserts each year. Machine operators work with many inserts each day, relying on their complex combination of chemistry and geometry to provide the cutting edges needed for precision, high speed production. Understanding how carbide tools are made and how the insert manufacturing processes influences their capabilities can help machine operators and manufacturers better understand their tools and overall processes.
To buy carbide inserts from our website, click here (westerntoolco.com)
![]() |
x |
What Carbide Inserts Are Made From
Most carbide inserts consist of cemented carbide, which is made from a combination of cobalt and tungsten carbide. Tungsten carbide's hard particles within the insert provide the insert with its qualities of hardness, and cobalt acts as the binding agent, holding the materials solidly together. The size of the tungsten grains being used affects the insert's hardness; larger grains (3-5 microns) result in softer, more quickly worn insert materials, while small grains (less than 1 micron) result in extremely hard, wear resistant inserts. The harder the tool, the more brittle it will be. When machining metals of exceptional hardness, harder inserts with smaller grains are typically used, while softer inserts are used most often in machining processes with interrupted cuts, which call for less brittle, tougher materials. The ratio of cobalt to tungsten carbide also influences carbide inserts' hardness levels; cobalt is softer, so the more cobalt an insert contains, the softer it will be.
The Insert Manufacturing Process
After the engineer has determined what level of hardness needs to be achieved, the manufacturing process starts with powdered raw materials. Powdered tungsten, cobalt and carbon are milled and blended together with alcohol and water, creating a thick slurry. This substance is put into a dryer, which evaporates the liquids, leaving a thoroughly mixed powder. Carbide inserts then undergo a sintering process in which they are mixed with a polymer to form a paste, pressed into insert-shaped dies and placed in a high-heat furnace to be sintered. The polymer is melted out of the inserts during this step, and the inserts shrink.
Coating Carbide Inserts
For most machining applications, coated carbide inserts are used. Coatings provide added levels of hardness and wear resistance which become necessary, especially during high-speed machining or machining of extremely hard metals. Most carbide tools are coated using chemical vapor deposition, in which a metal is ionized with electrical currents and applied to the inserts in the form of vaporized condensation. Another common process is physical vapor deposition, which creates thinner coating layers resulting in sharper cutting edges ideal for machining hardened steel and titanium.
Christopher Kyle is president of Knight Carbide, a Michigan-based manufacturer of tungsten carbide inserts. Knight Carbide specializes in custom insert engineering and manufacturing. To learn more about carbide insert technology, visit http://www.knightcarbide.com.
Article Source: http://EzineArticles.com/expert/Marjorie_Steele/724749
http://EzineArticles.com/?How-Carbide-Inserts-Are-Made&id=6212832
Welcome To Western Tool Company
Welcome to Western Tool Company in Arvada Colorado. We offer industrial supply and MRO products and we ship all over the United States. Our products include Hermes Abrasives, Sandpaper, random orbital discs,machining coolant, chlorine free coolant, sandpaper, sanding sponges, wide belt sandpaper, portable sanding belts, nonwoven abrasives, film back discs, foam sanding, velcro sandpaper,Chemetall, BASF, machining coolants, floor cleaners, defoamer, sump cleaners, chlorinated coolant , Hermes Abrasives, Surfprep and more! Visit our website for our complete catalog at westerntoolco.com
Subscribe to:
Posts (Atom)